Inconel 600 Tube is made based on Inconel 600 alloy, Inconel 600 is a nickel-chromium-iron austenite nickel-based alloy.
Nickel based Inconel 600 Tube is meant to be used at elevated temperature settings. Like most nickel alloys the ASME Sb163 600 Inconel Tube has the ability to withstand heat and has superior corrosion resistance property. In fact, the corrosion resistance property of Sb163 Inconel 600 Alloy 600 Seamless Tubing has been inherited from both nickel and chromium. Both these elements consist of the primary alloying content of ASTM B163 N06600 Alloy 600 Tubing. Therefore the Sb 163 UNS N06600 Alloy 600 Tube could be used in applications involving both condensers and heat-exchanger.
Inconel 600 Pipe is used for high temperature applications up to 2000F as well as cryogenic temperature applications. The material is highly weldable and has high corrosion resistance properties. The material has high carburization resistance and oxidation resistance. ZIZI is one of the leading manufacturers of the Inconel 600 Pipe products and a leading supplier.
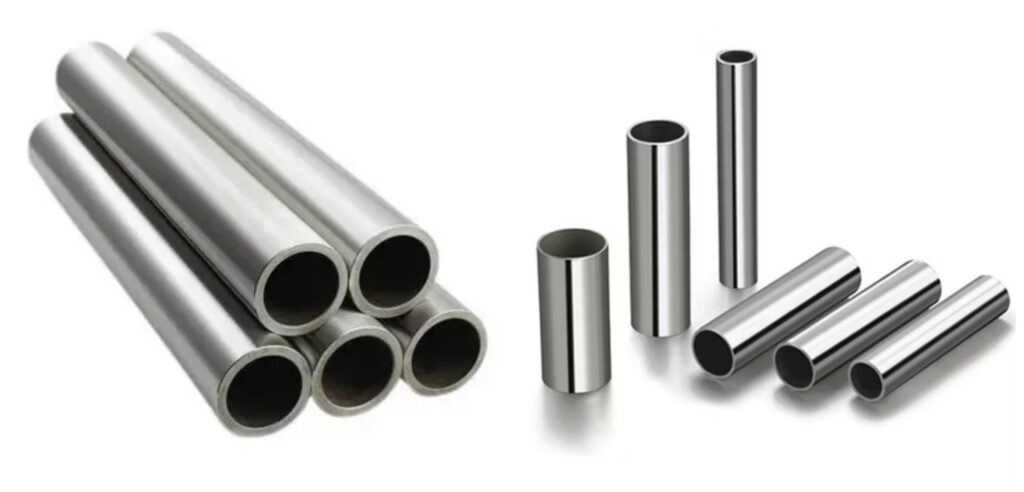
ASTM B163 N06600 Tubing Specification
Grades | Inconel 600 |
ASTM B163 uns n06600 | |
ASTM/ ASME Specification | ASTM B163 / ASME SB 163, ASTM B163 / ASME SB163 |
Standard Specification for Inconel 600 Seamless & Welded Superheater, Condenser, Hydraulic, Boiler and Heat-Exchanger Tubes | |
Shapes | ASTM B163 Alloy 600 Round, Rectangular, Square, Hydraulic, Straight, “U” Shape, Coiled, Honed Tubes, Pan Cake Coils |
Manufacturing Type | Seamless / ERW / Welded / Fabricated / CDW / CDS / DOM / CEW / 100% X Ray Welded Tube |
Thickness Range | SCH 5, SCH10, SCH 40, SCH 80, SCH 80S, SCH 160, SCH XXH, SCH XXS, SCH XS |
Delivery Condition | Annealed and Pickled (AP), Polished, Bright Annealed (BA), Cold Drawn, MF |
END | Plain End, Beveled End, Treaded 600 Inconel Tube |
Processing Service | Bending, Welding, Decoiling, Punching, Cutting, Moulding |
Technique | ASTM B516 Inconel 600 Cold drawn, Cold rolled, Hot rolled, Extrusion Tube |
Inconel UNS N06600 Tubing Packaging | Packed in PE Fabric Bundles or ply wooden box wrapped in plastic or Standard seaworthy export packing or as per customers’ request |
ASTM B163 Scope Standard
This specification covers seamless tubes of nickel and nickel alloys, as shown in Table 1, for use in condenser and heat-exchanger service.
This specification covers outside diameter and average wall, or outside diameter and minimum wall tube.
The sizes covered by this specification are 3 in. (76.2 mm) and under in outside diameter with minimum wall thicknesses of 0.148 in. (3.76 mm) and under, and with average wall thicknesses of 0.165 in. (4.19 mm) and under.
Terminology
Definitions: average diameter, n—average of the maximum and minimum outside diameters, as determined at any one cross section of the tube.
tube, n—hollow product of round or any other cross section having a continuous periphery.
Hydrostatic Test
Each tube with an outside diameter 1⁄8 in. (3.2 mm) and larger and tubes with wall thickness of 0.015 in. (0.38 mm) and over shall be tested by the manufacturer to an internal hydrostatic pressure of 1000 psi (6.9 MPa) provided that the fiber stress calculated in accordance with the following equation does not exceed the allowable fiber stress, S, indicated below. The tube shall show no evidence of leakage.
P = 2St/D
where:
P = hydrostatic test pressure, psi (MPa),
S = allowable fiber stress for material in the condition furnished, as follows:
t = minimum wall thickness, in. (mm); equal to the specified average wall minus the permissible “minus” wall tolerance, Table 4 and Table X2.2, or the specified minimum wall thickness, and
D = outside diameter of the tube, in. (mm).
ASTM B163 N06600 tube Chemical Composition
Grade | C | Mn | Si | Fe | S | Cr | Cu | Ni | |
Inconel 600 | min. | – | – | – | 6 | – | 14 | – | 72 |
max. | 0.15 | 1 | 0.5 | 10 | 0.015 | 17 | 0.5 | – |
ASTM B163 Alloy 600 Tubing Mechanical Properties
MATERIAL | T.S (MPA) | Y.S (MPA) | EL % | HARDNESS |
Inconel 600 | 80(552) | 35(241) | 30% | 102max |
Equivalent Grades of ASTM B163 Inconel 600 Tubes \ Pipe
STANDARD | WERKSTOFF NR. | UNS | JIS | BS | GOST | AFNOR | EN | OR |
INCONEL 600 | 2.4816 | N06600 | NCF600 | NA 14 | МНЖМц 28-2,5-1,5 | NC15FE11M | NiCr15Fe | ЭИ868 |
Is Inconel 600 better than hastelloy?
Inconel and Hastelloy are both excellent nickel-based alloys. It cannot be simply said that Inconel is better than Hastelloy, because they each have their own advantages and are suitable for different application scenarios. The performance depends on the specific use requirements and environmental conditions. The following is an analysis from different performance dimensions.
Mechanical properties
Inconel alloy: It has good strength and toughness at room temperature and can withstand large stress without cracking or excessive deformation. As the temperature rises, its strength decreases relatively slowly. It can still maintain certain mechanical properties in high temperature environments and has good high temperature strength and creep resistance.
Hastelloy alloy: The mechanical properties at room temperature are comparable to those of Inconel alloy, but in high temperature environments, the strength and creep resistance of Hastelloy alloy are more outstanding. This makes the application of Hastelloy alloy more advantageous under some extreme high temperature conditions.
Corrosion resistance
Inconel alloy: It has good tolerance to oxidizing environments and has good corrosion resistance in the atmosphere, water vapor and some oxidizing acids (such as nitric acid). Due to the chromium oxide protective film formed on the surface of the alloy by chromium elements, it can effectively prevent further intrusion of oxygen and other corrosive substances. In some environments with medium corrosion intensity, Inconel alloy can be used for a long time without obvious corrosion.
Hastelloy alloy: It is famous for its excellent corrosion resistance, especially in reducing environments and complex environments containing multiple corrosive media. It has extremely high corrosion resistance to non-oxidizing acids such as hydrochloric acid, sulfuric acid, phosphoric acid, and chloride solutions. In chemical production, various strong acids and complex chemical media are often encountered. Hastelloy alloy can remain stable under these harsh conditions, reduce the risk of corrosion and leakage, and ensure the long-term stable operation of production equipment.
Processing performance
Inconel alloy: The processing difficulty is relatively large. Due to its high strength and high toughness, special tools and processing techniques are required during mechanical processing (such as cutting, drilling, milling, etc.). During hot processing, the control requirements for temperature and processing speed are relatively strict to avoid cracks or other defects.
Hastelloy alloy: The processing performance is similar to that of Inconel alloy, and it also has a high processing difficulty. Because its composition contains more refractory elements, the hardness of the alloy is higher, which further increases the complexity of processing.
What is the difference between Inconel 600 and 750?
Processing Characteristics
Inconel 600: The processing characteristics of these alloys also differ. Inconel 600, with its good hot and cold workability, can be easily formed and welded using various techniques. Its excellent heat treatment stability ensures consistent properties after processing.
Inconel 750: possesses good workability, allowing it to be cut, welded, and bent without significant challenges. Its welding properties are particularly noteworthy, as it can be joined using various welding methods, such as tungsten inert gas welding and laser welding.
Corrosion resistance
Inconel 600: has good corrosion resistance, especially in oxidizing environments. In the atmosphere, water vapor and oxidizing acid (such as nitric acid) environment, a stable chromium oxide protective film can be formed on its surface to effectively resist corrosion. However, in some reducing environments containing specific corrosive media (such as high concentrations of chlorides), the corrosion resistance is relatively limited.
Inconel 750: The corrosion resistance is similar to that of Inconel 600, and it also performs well in oxidizing environments. Due to the optimization of composition, the stability of Inconel 750 in some complex corrosive environments has been improved, and its resistance to intergranular corrosion and stress corrosion cracking is relatively stronger. For example, in marine environments or certain chemical production environments, Inconel 750 is more resistant to cracking caused by the combined action of stress and corrosion than Inconel 600.
Application areas
Inconel 600: It is often used to manufacture parts that require a certain strength and good corrosion resistance in high temperature environments. In the chemical industry, it is used to manufacture equipment for handling corrosive media such as nitric acid and acetic acid, such as reactors and pipelines; in the power industry, it is used to manufacture heat exchangers, steam pipes, etc.; in the food processing industry, due to its good corrosion resistance and hygienic properties, it can be used to manufacture equipment that comes into contact with food.
Inconel 750: Due to its higher strength and creep resistance, it is more used in high-temperature environments that require harsh mechanical properties of materials. In the aerospace field, it is often used to manufacture engine parts, such as turbine blades and combustion chambers. These parts work under high temperature, high pressure and high stress conditions, and require materials to have excellent mechanical properties and stability; In the field of petrochemicals, high-temperature and high-pressure pipelines, reactors and other equipment, Inconel 750 is also widely used to ensure long-term reliable operation of equipment under harsh working conditions.
Permissible Variations
Permissible Variations for Small Diameter and Light Wall Tube (Converter Sizes)
NOTE 1—Ovality, Normal Wall Tube: As-Drawn (No. 2 and 3) Tempers—Ovality will be held within the outside diameter tolerances shown in the table. Annealed (No. 1) Temper—Ovality will be held within 2 % of the theoretical average outside diameter.
NOTE 2—Ovality Light Wall Tube: As-Drawn (No. 2 and 3) Tempers—Ovality will be held within 2 % of the theoretical average outside diameter. Annealed (No. 1) Temper—Ovality will be held within 3 % of the theoretical average outside diameter.
NOTE 3—Wall Tolerances, Light Wall Tube—The plus and minus wall tolerance shown in the table shall apply down to and including 0.005 in. (0.13 mm) in wall thickness. For wall thicknesses less than 0.005 in. the tolerance shall be plus and minus 0.0005 in.
Length,ft | Tube Size,in. | Permissible Variations,in. | ||||
Over | Under | |||||
U.S.Customary Units | ||||||
Under 1 | Up to 1.250,incl | 1/32 | 0 | |||
1 to 4,incl | Up to 1.250,incl | 1/16 | 0 | |||
Over 4 to 10,incl | Up to 1.250,incl | 3/32 | 0 | |||
Over 10 | Up to 1.250,incl | 3/16 | 0 | |||
Metric Units | ||||||
Length,m | Tube Sze,mm | Pemissible Variations,mm | ||||
Over | Under | |||||
Under 0.3 | Up to 31.75,incl | 0.794 | 0 | |||
0.3 to 1.2,incl | Up to 31.75,incl | 1.59 | 0 | |||
1.2 to 3.0,inc | Up to 31.75,incl | 2.38 | 0 | |||
Over 3.0 | Up to 31.75,incl | 4.76 | 0 | |||
Specified Outside Diameter,in. | Outside Diameter,in. | Inside Diameter,in | ||||
+ | – | + | – | + | – | |
U.S.Customary Units | ||||||
Under 3/32 | 0.002 | 0 | 0 | 0.002 | 10 | 10 |
to 3/16 (0.1875),exd | 0.003 | 0 | 0 | 0.003 | 10 | 10 |
3/16 to (0.500),excl | 0.004 | 0 | 0 | 0.004 | 10 | 10 |
1/2 to 1 1/4(1.250),incl | 0.005 | 0 | 0 | 0.005 | 10 | 10 |
Millimetres | ||||||
Under 2.38 | 0.051 | 0 | 0 | 0.051 | 10 | 10 |
2.38 to 4.76,excl | 0.076 | 0 | 0 | 0.076 | 10 | 10 |
4.76 to 12.70,exd | 0.102 | 0 | 0 | 0.102 | 10 | 10 |
12.70 to 31.8,incl | 0.127 | 0 | 0 | 0.127 | 10 | 10 |
What are the disadvantages of Inconel?
Although Inconel alloy has many excellent properties, it also has some disadvantages, as follows:
➪ Difficult processing
➪ Fabrication and Manufacturing Complexity
➪ Susceptibility to Certain Chemicals
➪ Work Hardening
➪ Machining challenges
➪ Complex hot processing
➪ Welding problems
➪ Hot cracking tendency
➪ Porosity and inclusions
➪ High Raw material cost
➪ Limited resistance to certain specific corrosion
➪ Specific strong corrosion environment
➪ Susceptibility to crevice corrosion and stress corrosion cracking
What are the advantages of Inconel?
Inconel is a series of nickel-based alloys. These alloys have many outstanding advantages, making them widely used in many fields:
➪ Excellent corrosion resistance
➪ Tolerance to oxidizing environments
➪ Adaptability to various corrosive environments
➪ Good high temperature performance
➪ High temperature stability
➪ Excellent low temperature performance
➪ Low temperature dimensional stability
➪ Good processing performance
➪ Hot processing performance
➪ Cold processing performance
➪ High weldability
What is Inconel 600 used for?
✮ The usual applications of Inconel 600 include:
✮ Gas turbine components
✮ Vegetable and fatty acid vessels
✮ Titanium dioxide
✮ Soap manufacture
✮ Phenol condensers
✮ MgCl2 evaporates
✮ Gasoline stabilizer production
✮ Furnace trays, mufflers, hangers
✮ Ethylene dichloride crackers
✮ Carburizing atmospheres
✮ Barge and tank truck liners
You can get an offer for products in below material forms:
-Pipe and Tube (EN 10216-5, ASTM A213, ASTM A249, A312, A790,)
-Forged Fitting and Flange (ASTM A182 , ASTM A105,ASTM B564 )
-Butt Weld Fittings (ASTM A234, ASTM A403,ASTM A815)
-Round bar , Billet (ASTM A276, ASTM A479)
– Plate, Sheet, Strip(ASTM A240, EN 10028-7, A480)
-Bolting, Nuts(ASTM A193, A194, A320)
Inconel 600 tube Exported Countries
We Export Inconel 600 tube to Saudi Arabia, United Arab Emirates, Qatar, Bahrain, Oman, Kuwait, Turkey, Egypt, Yemen , Syria, Jordan, Cyprus, Singapore, Malaysia, Indonesia, Thailand, Vietnam, South Korea, Japan, Sri Lanka, Maldives, Bangladesh, Cambodia, Argentina, Bolivia, Brazil, Venezuela, Colombia, Ecuador, Guyana, Paraguay, Uruguay, United States Of America, Canada, Mexico, Panama, Jamaica, Bahamas, Denmark, Norway, Germany, France,Italy, United Kingdom, Spain, Belgium, Greece, Czech Republic, Portugal, Hungary, Albania, Austria, Finland, Ireland, Croatia, Malta, Nigeria, Algeria, Angola, South Africa, Libya, Egypt, Sudan, Europe, Africa, Asia, North America, South America, Middle East.etc
Latest News
02 8 月 2019Copper Nickel Flanges UNS C70600Zizi offers ISO certified copper nickel flanges, stores large quantity of Cu-Ni 90/10 weld neck flan...
29 7 月 2019Stainless Steel Buttweld Fittings ManufacturerZizi is stainless steel buttweld fittings manufacturer, we offer stainless steel pipe elbow, tee, ca...
19 7 月 2019Steel Pipe Nipple Types, Dimensions and MaterialsBasic pattern of steel pipe nipple is a short piece of pipe with threads at both end or at one end....