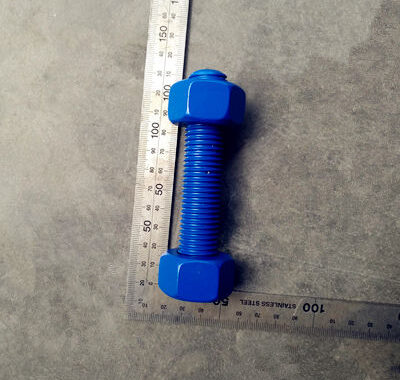
Surface Treatment of Fasteners
There are nine types of Fastener Surface Treatment, like Electro-Zinc, Phosphating, Oxidation (Blackening), Cadmium(Electro) Plating, Electrochromism, Silver and Nickel Plating, Hot-Dip Zinc, Zinc Infiltration and Dacromet
Electro-Zinc
Electro-Zinc is the most commonly used Fastener Surface Treatment for commercial fasteners. It is cheaper and good looking, colors are black or military green. However, its anti-corrosion performance is so so and the zinc coating layer is thin. Generally, electro-galvanized neutral salt spray test should be took within 72 hours. There are also special sealants, making the neutral salt spray test up to 200 hours. But it is expensive, and can only support galvanizing 6 times. Electro-Zinc processing is easy to produce hydrogen embrittlement, so more than 10.9 bolts do not need galvanizing.
Electro-Zinc Application
The hydrogen must be plating before passivation because the passivation film will be destroyed in 60 ℃ and above.Therefore, it has poor operability and high processing cost. In reality, the general production plant will not take the initiative to hydrogen, unless the customers have mandatory requirements. The fastener torque-preload force of electroplating zinc is poor in consistency and unstable, so it is not used in the connection of important parts generally. However, the method of coated lubricating material can help to improve the consistency of torque-preload.
Phosphating
Phosphating is cheaper than zinc plating but its corrosion resistance is worse. After phosphating,the fittings should be oiled. Therefore, the performance of corrosion resistance has a great relevant with the anti-rust oil. For example, after general phosphating coating and oiling, neutral salt spray test only needs 10-20 hours. But if the anti-rust oil is high-grade, it can reach 72-96 hours. However, the price is higher. Lubrication performance of zn-Series Phosphating is better than manganese system phosphating, while manganese system phosphating has better corrosion resistance, and wear resistance.
Phosphating Application
Its working temperature is 225 degrees Fahrenheit to 400 degrees (107 to 204°), and industrial fasteners need phosphating oil treatment more often. Because of its torque a p reload consistency is good, the assembly can meet the design expected tightening requirements, so in industry it uses more often, especially in the connection of important parts, such as the connecting rod bolts, nuts, cylinder heads, main bearings, flywheel bolts, wheel bolts and nuts, etc. The surface of high-strength bolts may have hydrogen embrittlement problem after phosphating.
Oxidation (Blackening)
Blackening oil is a popular fastener surface treatment for industrial fasteners because it is the cheapest and looks good before the oil runs out. Because there is almost no rust-proof ability, it will soon rust without oil. In the presence of oil, the salt spray test can only reach 3-5 hours. Black Fasteners Torque-preload consistency is also poor. If you need to improve, you can apply grease to the thread when assembling and then spin.
Cadmium(Electro) Plating
The corrosion resistance of cadmium coating is very good, especially in the marine atmosphere environment, the corrosion resistance is better than other surface treatments. Electroplating cadmium processing process of waste liquid treatment costs, high cost, the price of zinc electroplating is about $number times. Therefore, in the general industry is not used, only for a specific environment. For example, for the oil drilling platform and the HNA aircraft used fasteners.
Electrochromism
Chromium coating is a very stable fastener surface treatment in the atmosphere, not easy to change color and loss of luster, high hardness and wear resistance. Chrome plating on fasteners is generally used as a decorative function. It is rarely used in industrial areas where corrosion resistance is high, because good chrome plated fasteners are as expensive as stainless steel, but only when stainless steel is not strong enough to be replaced with chrome fasteners. In order to prevent corrosion, chrome plating should be first plated with copper and nickel. Chromium coating can withstand the high temperature of 1200 degrees Fahrenheit (650 ℃). But it also has the same hydrogen embrittlement problem as electroplating zinc.
Silver and Nickel Plating
Fastener Surface Treatment of Silver coating can be anti-corrosion, and can be used as a solid lubricant fasteners. For cost reasons, the NUT is silver plated, bolts are not used, and sometimes small bolts are silver plated. Silver loses luster in the air, but can function under 1600 degrees Fahrenheit. Therefore, people use its high temperature and lubrication characteristics, to work at high temperature fasteners to prevent the bolt, nut oxidation bite dead. Fasteners Nickel-plated, mainly for both anti-corrosion and good conductivity of the place. such as vehicle battery extraction terminals.
Hot-Dip Zinc
Hot-dip zinc is coating fittings with liquid zinc. Its coating thickness is 15 to 10μm which is difficult to control. But it has good corrosion resistance, and very common in engineering.
The pollution during hot-dip galvanizing is serious, such as zinc scrap and zinc vapor. And due to the thickness of the coating, it is difficult to rotate the internal and external thread of fasteners. Luckily, there are two ways to resolve this problem. One is to attack the internal thread after plating to solve the problem, and it also reduces the antiseptic performance. The other is in the nut tapping, so that the thread is larger than the mark of 0.15 to 0.75mm (M5-M30), and then hot dip zinc.
Hot-Dip Zinc Application
Currently there is a loose thread, the United States “in the” internal thread can solve this problem. Because the internal thread and the outer thread are not fastened when the gap is large, so accommodate the thick coating can be used. It does not affect the rotation, while the anti-corrosion performance and strength also remain intact and unaffected. Because of the temperature of hot dip zinc, it can not be used for fasteners above Grade 10.9
Zinc Infiltration
Zinc infiltration is a zinc powder solid metallurgical thermal diffusion coating. Its uniformity is good, the thread, the blind hole can obtain the uniform layer. The coating thickness is 10~110μm and the error can be controlled at 10%. Its adhesion to the matrix and anti-corrosion properties in the zinc coating (galvanized, hot dip zinc, dacromet) is the best. Its processing process non-polluting, the most environmentally friendly.
Dacromet
There is no hydrogen embrittlement problem, and the torque-preload force is good for consistent performance. If you do not consider the environmental problems of hexavalent chromium, it is actually the most suitable for high strength fasteners.
Latest News
02 8 月 2019Copper Nickel Flanges UNS C70600Zizi offers ISO certified copper nickel flanges, stores large quantity of Cu-Ni 90/10 weld neck flan...
29 7 月 2019Stainless Steel Buttweld Fittings ManufacturerZizi is stainless steel buttweld fittings manufacturer, we offer stainless steel pipe elbow, tee, ca...
19 7 月 2019Steel Pipe Nipple Types, Dimensions and MaterialsBasic pattern of steel pipe nipple is a short piece of pipe with threads at both end or at one end....